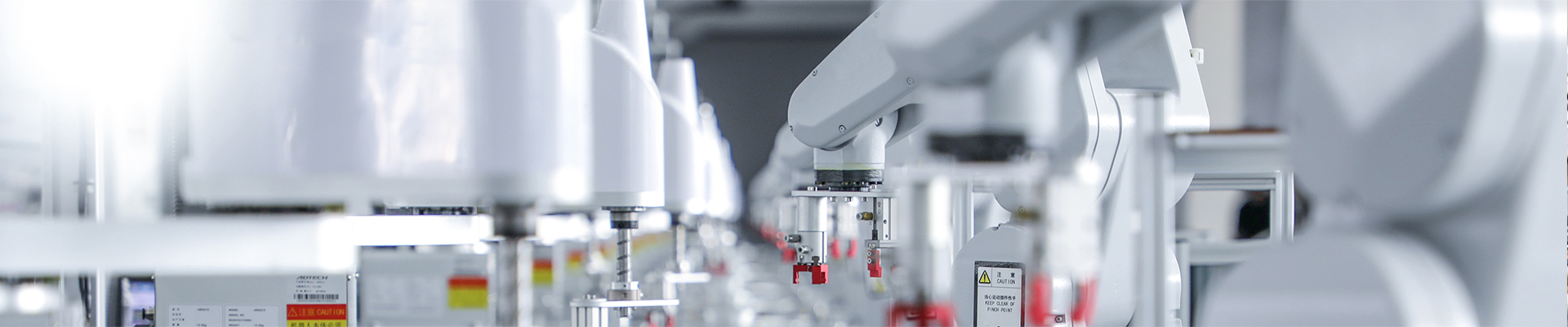
high frequency automotive carpet welding equipment
2025-05-16 14:08Overview of high frequency automotive carpet welding equipment
High frequency automotive carpet welding equipment is an advanced equipment specially used for automotive carpet welding. It uses the action of high frequency electromagnetic fields to enable carpet materials to reach high temperatures in a short time, thereby achieving the purpose of welding. This equipment has the advantages of high efficiency, precision and stability, and can greatly improve the production quality and production efficiency of automobile carpets.
How it works
The working principle of high frequency welding equipment is based on high frequency induction heating technology. The device generates a high frequency alternating current through a high frequency generator, which generates a high frequency electromagnetic field through the induction coil. At the same time, the polymer materials in the carpet will soften and fuse at high temperatures to achieve welding.
Equipment structure
High frequency generator: It is the core component of high frequency welding equipment, responsible for generating high frequency alternating current. It is usually composed of power supply circuits, oscillation circuits, control circuits, etc., which can accurately control the frequency, power and time of the output high frequency current to meet the requirements of different welding processes.
Mold: It is a component that generates a high frequency electromagnetic field. Its shape and size are designed according to the welding parts and shapes of the carpet. The molds of high frequency automotive carpet welding equipment are generally made of high temperature resistant and high strength copper, and are cooled with water inside to ensure stability and service life under high load working conditions.
Welding workbench: used to place carpets, usually with adjustable fixtures that can hold the carpet’s position to ensure the accuracy and consistency of welding. The workbench of the high frequency automotive carpet welding equipment is also equipped with temperature sensors and pressure sensors to monitor the temperature and pressure changes during the welding process in real time and feed it back to the control system for adjustment.
Control system: It is the brain of high frequency welding equipment. It realizes the automation of the entire welding process through coordinated control of various components such as high frequency generators, presses, welding workbenches, etc. The control system can accurately control the welding process based on preset welding parameters, such as welding time, temperature, pressure, etc., and also has fault diagnosis and alarm functions, which can promptly detect and deal with problems during the operation of the equipment.
Features of high frequency automotive carpet welding equipment
Fast welding speed: High frequency induction heating can make the carpet material reach the temperature required for welding in a short time, greatly shortening the welding time and improving production efficiency. Compared with traditional welding methods, such as hot press welding, ultrasonic welding, etc., the welding speed of high frequency welding equipment can be increased several times or even dozens of times.
High welding quality: Since high frequency heating directly generates heat inside the material, the temperature distribution in the welding area is evenly distributed, and there will be no local overheating or supercooling, thus ensuring the quality of the welding. The welded carpet welds are firm and beautiful, without obvious welding marks, and can also maintain the original performance and appearance of the carpet.
Strong adaptability: High frequency automotive carpet welding equipment can flexibly adjust welding parameters, such as frequency, power, time, etc. according to different automotive carpet materials and welding requirements. Whether it is a single layer carpet or a multi layer composite carpet, whether it is an ordinary chemical fiber carpet or a carpet with special functions, such as anti static, sound insulation, heat insulation, etc., it can be welded with high quality through this equipment.
Energy saving and environmental protection: High frequency induction heating is a non contact heating method that does not require heat transfer through the heating medium, so the heat loss is small and the energy utilization rate is high. Compared with traditional heating methods, high frequency welding equipment can save about 30% 50%. At the same time, high frequency welding equipment will not produce harmful gases and waste during work, and will not pollute the environment.
High degree of automation: High frequency automotive carpet welding equipment adopts advanced control systems, which can realize automated control of the welding process. From loading, positioning, welding to laying of carpets, the entire process can be automatically completed through preset procedures, reducing the error and labor intensity of manual operations and improving the stability and consistency of production.
Application areas
High frequency automotive carpet welding equipment is mainly used in the automobile manufacturing industry and is used in the production and processing of automotive carpets. It can weld various types of carpets, including carpets of different models such as cars, buses, trucks, etc. At the same time, this equipment can also be used in other areas of automotive interior parts, such as welding of door interior panels, seat covers, etc.
UNIFY high frequency automotive carpet welding equipment has become an indispensable and important equipment in the automobile manufacturing industry with its advanced technology, efficient performance and excellent quality, and plays an important role in improving the quality and production efficiency of automobile interiors.