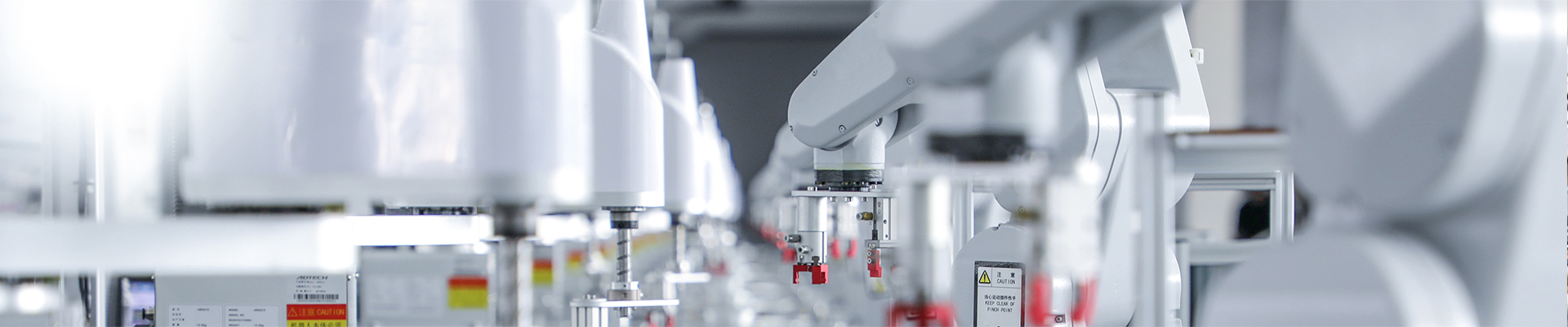
The rapid mold change technology of high frequency welding machine
2025-05-14 16:56The rapid mold change technology of high frequency welding machine is a key means to improve production efficiency and enhance machine flexibility.
Quick mold change, or SMED (Single Minute Exchange of Die), aims to minimize the replacement time of high frequency welding machine molds, in minutes or even seconds. In the field of high frequency welding machine, the traditional mold replacement process is cumbersome and time consuming. After shutdown, it is necessary to manually disassemble the old mold, clean the machine interface, install the new mold and perform debugging and calibration. The entire process often takes several hours, which seriously affects the production continuity and machine utilization rate.
The rapid mold change system of UNIFY high frequency welding machine starts from multiple aspects of hardware and software. In terms of hardware, standardized and modular mold design is adopted. All types of mold interfaces are uniformly specified and equipped with fast positioning and locking devices. For example, hydraulic or pneumatic fast chucks can be used to tighten and loosen the mold within a few seconds, greatly saving installation and disassembly time. At the same time, high frequency welding is equipped with a movable mold storage rack, and the mold to be replaced is prepared in advance before changing the mold, so that it can be switched quickly when changing the mold. In terms of software, through advanced control systems, the welding parameters corresponding to different molds are stored. After the mold change is completed, the new mold parameters are called with one click, and the device will automatically complete the parameter adjustment without manual reset and repeated debugging.
After using the rapid mold change technology, the mold change time of UNIFY high frequency welding machine can be sharply reduced from the original few hours to more than ten minutes or even shorter. This not only greatly improves the production efficiency of machine and reduces the capacity loss caused by shutdown and mold replacement, but also allows enterprises to quickly respond to market diversified needs, flexibly adjust production products, and gain an advantage in the modern production model of small batches and multiple varieties.
Another advantage of the rapid mold change system is that the mold position is more accurate and can adapt to high-precision welding. The rapid mold change system is used in UNIFY's equipment for high-frequency automotive carpet welding equipment, automotive sun visor high-frequency welding equipment, membrane material high-frequency welding equipment, turntable high-frequency equipment, medical product high-frequency welding equipment, etc.