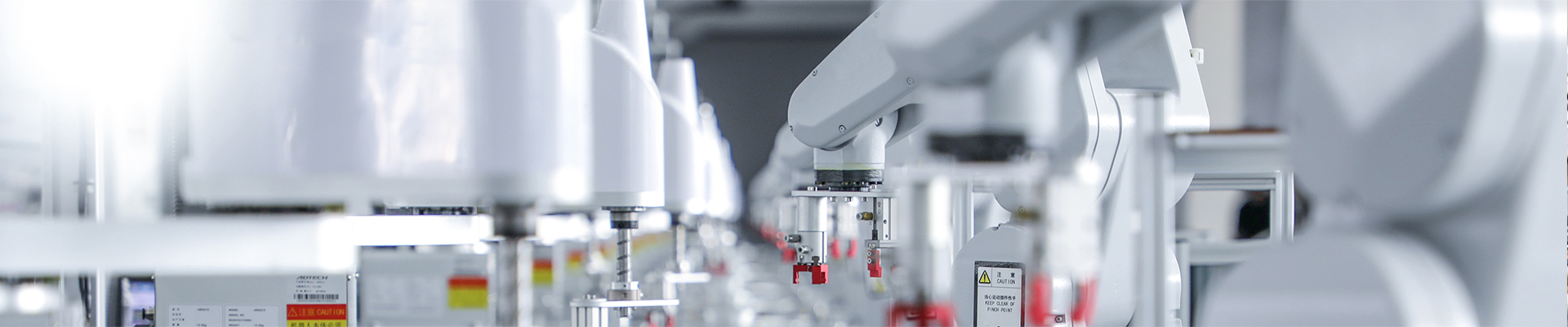
high frequency welding equipment
2025-05-09 16:53The automatic power tracking function of high frequency welding equipment plays a key role in improving welding quality and efficiency.
During high frequency welding, factors such as the material, shape, size, and welding environment of the welding object will constantly change, which will lead to dynamic changes in the welding load. For traditional high frequency welding equipment, if the power cannot match these changes in real time, it is easy to cause problems such as poor welding, over-welding or equipment failure.
UNIFY power automatic tracking technology can monitor various parameters during welding in real time by introducing advanced sensors and intelligent control systems. Among them, the current sensor and voltage sensor closely monitor the current and voltage values output by the high frequency welding equipment and feed them back to the control system. The control system uses complex algorithms to quickly calculate the current actual power and compare it with the preset optimal welding power. Once the two are deviated, the control system immediately issues instructions to accurately adjust the output of the high frequency power supply.
This regulation process involves multiple key links. In the inverter section, the output voltage is changed by changing the on and off time of the power device, that is, adjusting the duty cycle of the pulse width modulation (PWM) signal, and thus changing the output power. For some high frequency devices that use frequency adjustment, the control system will change the operating frequency of the oscillation circuit to adapt to load changes and achieve automatic power matching.
Automatic power tracking technology brings many advantages. In terms of improving welding quality, no matter how the welding object changes, it can ensure that the power is always maintained at the appropriate level, making the welds uniform and firm, reducing bad phenomena such as false welding and de-welding, and significantly reducing product waste rate. In order to improve production efficiency, high frequency welding equipment does not need to be frequently shut down and adjusted due to power mismatch, the continuous operation capacity is enhanced, and the production pace is accelerated. From the perspective of protection of equipment, it avoids damage to caused by power overload or underload, extends the service life of equipment, and reduces maintenance costs and downtime.
UNIFY equipment with automatic power tracking can ensure consistent welding quality in all places. UNIFY power automatic tracking technology is the key to ensuring welding quality and stability, and meets strict industry standards.
Power automatic tracking technology in UNIFY series of products is mainly used in automotive carpet high frequency welding equipment, automotive sunshade welding equipment, film welding equipment.